Introduction
Diesel generators are essential power sources in various industries, providing backup power during outages or serving as the primary power supply in remote locations. However, when operating in corrosive atmospheres, such as those found in marine environments, chemical plants, or offshore oil rigs, diesel generators face unique challenges that can affect their performance and reliability. In this article, we will explore the impact of corrosive atmospheres on diesel generators and discuss the measures that can be taken to ensure their efficient operation in such environments.
Understanding Corrosive Atmospheres
Corrosive atmospheres are characterized by the presence of corrosive elements such as saltwater, chemicals, or gases that can degrade the materials of equipment exposed to them. In marine environments, for example, saltwater spray can cause rapid corrosion of metal components, while chemical plants may release corrosive gases that can damage sensitive electronics. These corrosive elements can accelerate wear and tear on diesel generators, leading to premature failure and costly downtime.
Impact of Corrosive Atmospheres on Diesel Generators
1. Corrosion of Metal Components
One of the primary concerns when operating diesel generators in corrosive atmospheres is the corrosion of metal components. The exposure to saltwater, chemicals, or gases can cause rust and corrosion on surfaces such as the engine block, exhaust system, and fuel lines. This corrosion can weaken the structural integrity of the components, leading to leaks, malfunctions, and ultimately, the failure of the generator.
2. Degradation of Electrical Components
In addition to metal components, electrical components of diesel generators are also vulnerable to corrosion in corrosive atmospheres. The presence of moisture, salt, or chemicals can cause degradation of wiring, connectors, and circuit boards, leading to electrical faults and malfunctions. This can result in erratic operation, voltage fluctuations, and even electrical fires, posing a significant safety hazard.
3. Reduced Performance and Efficiency
Corrosion and degradation of components can also impact the performance and efficiency of diesel generators operating in corrosive atmospheres. As components wear out prematurely, the generator may experience decreased power output, increased fuel consumption, and reduced overall efficiency. This can result in higher operating costs, reduced reliability, and compromised power supply during critical situations.
Mitigating the Effects of Corrosive Atmospheres
To ensure the reliable operation of diesel generators in corrosive atmospheres, several measures can be taken to mitigate the effects of corrosion and protect the equipment from damage. These measures include:
1. Material Selection
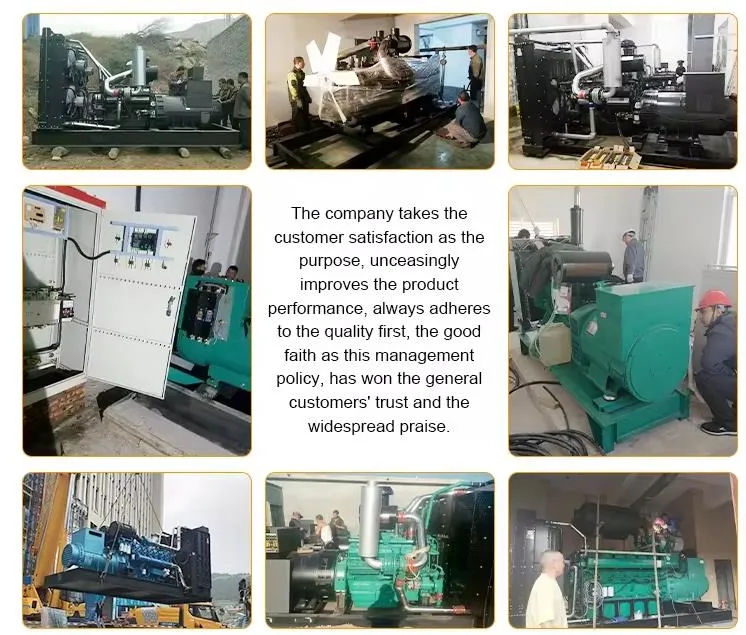
Choosing corrosion-resistant materials for critical components of diesel generators is essential for ensuring their longevity in corrosive atmospheres. Stainless steel, aluminum, and corrosion-resistant coatings can help protect metal surfaces from rust and corrosion, while specialized seals and gaskets can prevent moisture and contaminants from entering sensitive areas.
2. Regular Maintenance
Regular maintenance and inspection of diesel generators are crucial for detecting and addressing corrosion issues before they escalate. Cleaning components, replacing worn parts, and applying protective coatings can help prolong the life of the generator and prevent costly repairs or downtime. Additionally, monitoring systems can alert operators to potential corrosion-related problems, allowing for timely intervention.
3. Environmental Protection
Creating a protective environment around diesel generators can help shield them from corrosive elements in the atmosphere. Enclosures, shelters, or barriers can be installed to minimize exposure to saltwater, chemicals, or gases, while ventilation systems can ensure proper airflow and prevent the buildup of moisture. Proper drainage and waterproofing measures can also help prevent water ingress and corrosion damage.
4. Corrosion Inhibitors
Applying corrosion inhibitors to metal surfaces can help prevent rust and corrosion in diesel generators exposed to corrosive atmospheres. These chemical compounds form a protective barrier on metal surfaces, inhibiting the oxidation process and extending the life of the components. Regular application of corrosion inhibitors can provide an additional layer of protection against corrosion-related damage.
5. Monitoring and Testing
Implementing a comprehensive monitoring and testing program can help identify corrosion issues early on and prevent catastrophic failures in diesel generators. Regular inspections, testing of electrical systems, and analysis of lubricants and fuel can help detect corrosion-related problems before they compromise the performance of the generator. Advanced diagnostic tools, such as vibration analysis and thermal imaging, can also provide valuable insights into the condition of the equipment.
Conclusion
Diesel generators play a critical role in providing reliable power generation in a wide range of applications, including corrosive atmospheres. By understanding the impact of corrosion on diesel generators and implementing preventive measures to protect the equipment from damage, operators can ensure the efficient operation of their generators in challenging environments. With 75kw diesel generator for emergency backup , regular maintenance, environmental protection, corrosion inhibitors, and monitoring and testing, diesel generators can withstand the corrosive effects of saltwater, chemicals, and gases, and continue to deliver reliable power when needed most.